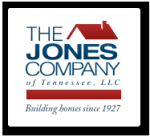
Business ProfileforThe Jones Company of Tennessee, LLC
At-a-glance
Related Categories
BBB Business Profiles may not be reproduced for sales or promotional purposes.
BBB Business Profiles are provided solely to assist you in exercising your own best judgment. BBB asks third parties who publish complaints, reviews and/or responses on this website to affirm that the information provided is accurate. However, BBB does not verify the accuracy of information provided by third parties, and does not guarantee the accuracy of any information in Business Profiles.
When considering complaint information, please take into account the company's size and volume of transactions, and understand that the nature of complaints and a firm's responses to them are often more important than the number of complaints.
BBB Business Profiles generally cover a three-year reporting period. BBB Business Profiles are subject to change at any time. If you choose to do business with this business, please let the business know that you contacted BBB for a BBB Business Profile.
As a matter of policy, BBB does not endorse any product, service or business. Businesses are under no obligation to seek BBB accreditation, and some businesses are not accredited because they have not sought BBB accreditation.